〈一〉、封边有花斑、气泡1、材料因素。如PT、NY等吸湿性材料在保存时易吸收水分,在高温制袋时易产生气泡、气斑。另外复合粘合剂因尚未完全固化,在高温热封时耐温不够、剥离强度差,也易脱层产生气斑。2、热封边部位较宽时易产生气斑,应调整压力,调大间隙,将夹气挤掉。薄膜走动时有波动会夹进空气,进刀前应排干净,进热封刀前夹板应适当夹紧。3、制袋控制不当,如硅橡胶板长时间使用变形、高温布破损、热封刀上有脏物等。制袋速度、温度、压力等工艺参数不适当和不协调也会产生气斑。
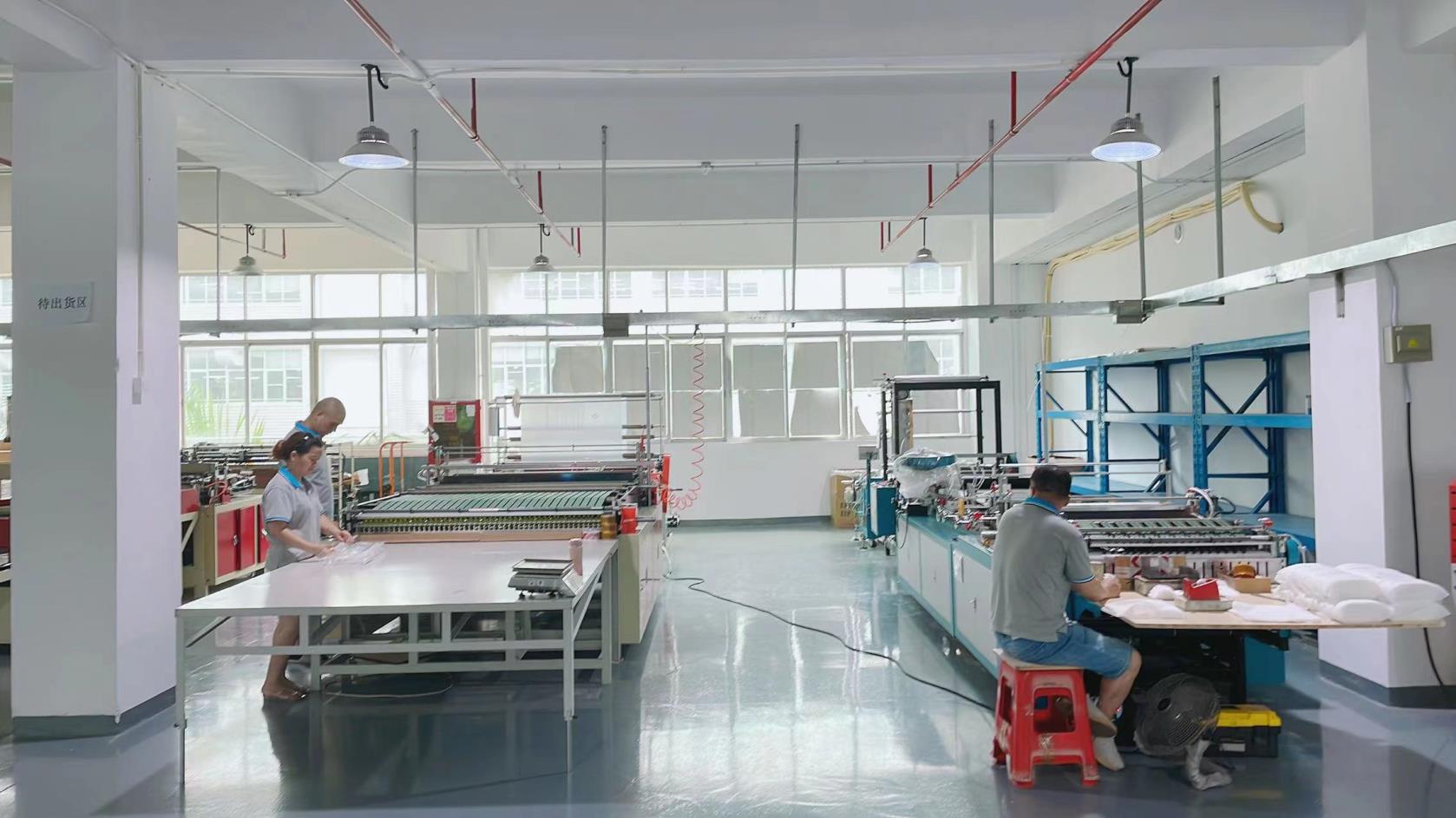
〈二〉、热封强度差热封强度差是制袋过程中最常出现的疑难问题。1、热封材料的影响热封材料的种类不同,热封强度不同,如PP、PE、EVA热封强度不一致;同种薄膜不同聚合方法的产品,热封强度不同;材料的厚度、均匀性等也会影响热封强度;热封层不同的加工方法,如吹塑、流延膜等,均影响热封强度。薄膜的保存时间过长,析出物增多,经过电晕处理热封强度差。吸湿性材料吸潮,热封面脱层,剥离强度下降。2、复合膜加工工艺的影响印刷油墨耐温性差或在油墨中添加剂不适当,在制袋高温下,印刷层发生脱层,热封强度下降。热封边应尽量设计成无图案。复合工艺中粘合剂选择也很重要,粘合剂的配比、粘度等参数的合理与否均会影响封口强度。在挤出复合或涂布工艺中,加工温度高,材料表面氧化程度大,羧基生成量增加,不利于热封。3、制袋工艺的影响热封后的封边冷却不够,定型不足,不能消除内应力,影响强度及外观,应及时检查,加强冷却水循环系统。热封次数越多,热封强度越高。纵向热封次数取决于纵向焊刀的有效长度和袋长之比;横向热封次数由机台横向热封装置的组合数决定。良好的热封,要求热封次数至少在两次以上。
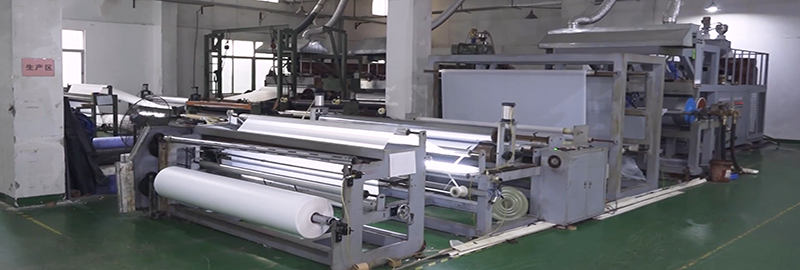
〈三〉、热封处脆弱1、原因:热封压力过大,热封时间过长或热封温度过高,热封线边缘被挤薄。解决:将压力、温度和时间调整至适当。2、原因:薄膜强度差。解决:①、选用强度好的薄膜。②、复合袋的内层薄膜可选用吹塑薄膜,因为吹塑薄膜的强度比流延薄膜要好。③、对用于蒸煮的复合袋,其内层薄膜厚度不要小于0.07毫米3、原因:热封线未冷却时受力。解决:避免热封线拉长或拉薄。4、原因:热封温度过低。解决:①、提高热封温度。②、增加热封时间。5、原因:热封压力过低。解决:提高热封压力。6、原因:热封刀棱角太锋利,热压时对材料进行了根切。解决:打磨热封刀棱角。
〈四〉、封口膜皱、翘曲1、热封温度过高,引起不均衡收缩。2、热封时间太长,间接导致温度积累,使膜表面过热。3、制袋张力控制不当,影响了薄膜的平整度,破坏了间隙送料的均衡性。4、间隙偏大,最好控制在1~1.5mm之间。
〈五〉、裁切线与横封边不平齐1、裁切刀的下刃装得太低。2、切刀下面导梳变弯,高于下刀位置。3、切刀基座安装不平齐。
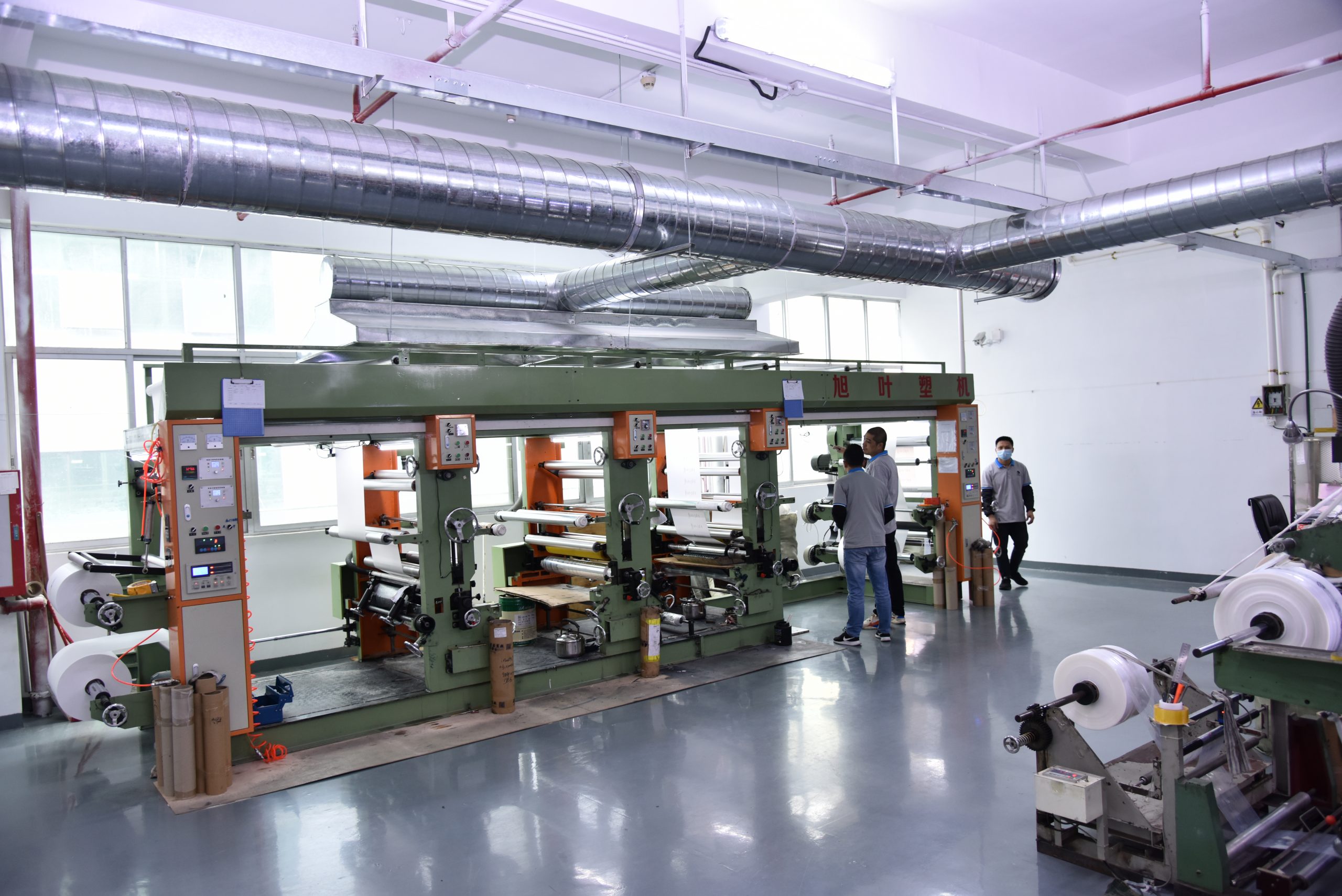
〈六〉、上下片对不准1、材料的厚度不均匀,有松弛现象。2、浮动辊张力太小。3、运行过程中有些辊转动不平衡。弯,高于下刀位置。4、切刀基座安装不平齐。
〈七〉、热封处不均匀1、原因:温度控制不适宜。解决:①、热封工具的温度应均匀一致,其相差不要超过±5℃ 。②、检查:温度控制器的灵敏度,不要大于5℃。2、原因:加热压力不均匀解决:①、加热工具与衬垫面应平行,接触处要保持清洁。②、薄膜的厚薄误差要小。
〈八〉、开口性差1、原因:印刷后薄膜未冷却。解决:卷取前应充分冷却。2、原因:卷取张力过大。解决:①、降低卷绕张力。②、卷取前应充分冷却薄膜。3、原因:薄膜双面经过电晕处理。解决:只对印刷、复合面进行电晕处理。4、原因:薄膜的开口性差。解决:选用含有抗粘连剂的薄膜。5、原因:袋口的切断线与热封线太近。解决:切断线应离开热封线2–3mm以上。6、原因:复合袋的开口性差。解决:①、内层薄膜选用吹塑薄膜。②、在固化时烘箱温度不要超过60℃。③、制袋前薄膜应充分冷却。
〈九〉、复合材料热合处分层1、原因:热封部分有印墨存在是产生分层的最主要的原因。解决:在印刷前要预先设计好,避免在热封处有印墨出现。2、原因:油墨的耐热性差解决:①、使用耐热性好的油墨。②、在印刷前,薄膜进行表面处理,以提高油墨的附着力。3、原因:内外层温度相差太大。解决:①、降低加热温度,并降低制袋速度。②、在热封前,先进行预热。
〈十〉、油墨脱落1、原因:在热封处有印墨存在。解决:在热封处应避免有印墨的存在。2、原因:油墨的耐热性差。解决:选用耐热性好的油墨。3、原因:使用网格型热封工具。解决:①、改用平面型热封工具。②、在热封工具下贴一张聚四氟乙烯薄片。4、原因:对于铝箔复合材料,即使表层没有软化,但AC剂和印墨已熔化,因而成皮膜状脱落。解决:
①、使用耐热性好的AC剂和印墨。②、降低热封温度,延长热封时间。
生物降解袋与PE袋切袋时的温度不同。