生物降解挤出造粒常见的问题有:断条,冒料,粒子外观不光滑,有黑点,下面就这几个常见问题点进行分析及如何解决。
A.断条
1.原料有杂料,检查下料口的物料中是否含有杂料;
2.塑化不良,需提高加工温度。(对于玻纤增强复合材料而言,往往是由于温度过高引起的)抽真空的力度不够,检查真空的运转是否良好,密封是否达到要求;
3.过滤网堵塞,换过滤网;
4.口模孔数不对,料流失衡;
5.未加多孔板(玻纤类产品除外),熔体扰动而造成断条,断条主要集中在左侧;
6.挤出压力太低,螺杆内的物料不充实,需提高喂料频率、加大过滤网目数。
B.冒料
1.适当降低喂料量或者降低螺杆转速
2.升高前面段的温度,加快物料在机筒中的塑化;如增强料玻纤口前后的常规调节:输送及其熔化区温度适当提升5-10℃,将玱纤口后加热区温度适当调低10-20℃;
3.调整前面的螺杆组合,使前后输送平衡杆加快物料在杆筒中的塑化。
C.粒子外观不光滑
1.粒子两端的有孔问题:两端都有孔:说明料里含的低分子物质的水份较多,真空排气没抽干净或原料含的低分子水分较多。只有一端有孔:说明料里含的低分子物质水份较少,没有严格要求时可以接受。解决:前处理(干燥、密封等);加强真空排气(要考虑到螺杆设计);提高水槽温度。
2.粒子发泡:出现多个孔,或者表面粗糙真空度不够;温度过高,原料成分的分解等。原料含水分过高;原料(较差的副牌料)不耐温或成分使用不当,相互间化学反应而发;
3.颗粒表面光滑平整问题:颗粒表面光滑平整,要看所用的原材料的成分——玻纤、 无机矿物、表面较粗燥的阻燃剂等物质。但相比对下, 同料批次有差异,原因有:
① 塑化混炼不好,交叉分布不够细加工温度不够,塑化不好;
② 机器问题,如模孔不平整、不够光滑等;
③ 原料成分间相容性不好(也包括色粉色母在内),出现分层、析出等。
4.粒径:长短基本一致(有长粒、短粒)料条交叉迚入切粒机;料条交叉迚入切粒机;压辊太松(切粒机气压);切刀锋利度,调节切刀刀距、刮刀与花键轴间隙。
5.长条:长度大于标准粒径2倍以上水分调节(特别是5000体系,水分过多料条有滑手感)压辊太松(切粒机气压);切刀锋利度,调节切刀刀距、刮刀与花键轴间隙。动刀或胶辊已经严重磨损,需要更换.
6.粉末:用干净的手抓一把料粒放开后看手掌上残留的粉末适当少过水,调节切条温度动刀锋利度、定刀和滚刀的间隙(0.07-0.15MM间)增强产品无真空戒真空不良
7.粘结、焦烧过水太少切粒机牵引过快无吹风机,或者吹风机的风力太弱
8.连粒、粘粒切条的温度过高调节过水长度、或调节切粒机转速料条在过水时即交叉粘连,或者料条交叉进入切粒
9.尾巴切刀不锋利颗粒本身存在裂纹
10.铁锈:粒子表面有红褐色的物质,主要为料条水分过多,风干不够导致切粒机内刀具生锈所致。减少过水加多风刀数量(或者加大吹风力度)
D.黑点
1.粒子表面有不可抹去的黑点清洗机不干净;真空口、玻纤口、模头上、滤板上残留、 滞留、高温炭化的物料带入;温度过高导致螺杆、螺筒内物料炭化;阻燃剂高温分解、炭化;色粉分散不良原材料等级不够,黑点多;
2..变色/黑、黄线条/油污粒子:真空口内蒸汽物掉入;模头、机头、滤板上滞留物质炭化;阻燃剂分解、炭化;停机时间过长物料分解;料条所经区域油污粘附;
3.粒子表面有可抹去的黑点水槽是否清理干净料筒、接料斗、振动筛等未清理干净环境中引入黑点是物料在机筒中炭化导致,这机筒在玱纤口和真空口处有炭化的物料,需要清理玻纤口和真空口,还有是口模和网板的地方有炭化物料,需要卸下口模清理。
因压力不稳定而导致的黑点
A.当配方中有几种MI不同的物料时,螺杆设计应当按照最低粘度的物料,并且相对最强的剪切
B.定期清理筛网、排气口、真空口、拔螺杆
C.选用含低摩擦系数涂层的螺杆
D.引入熔体泵
深圳市久信达科技有限公司降解袋:
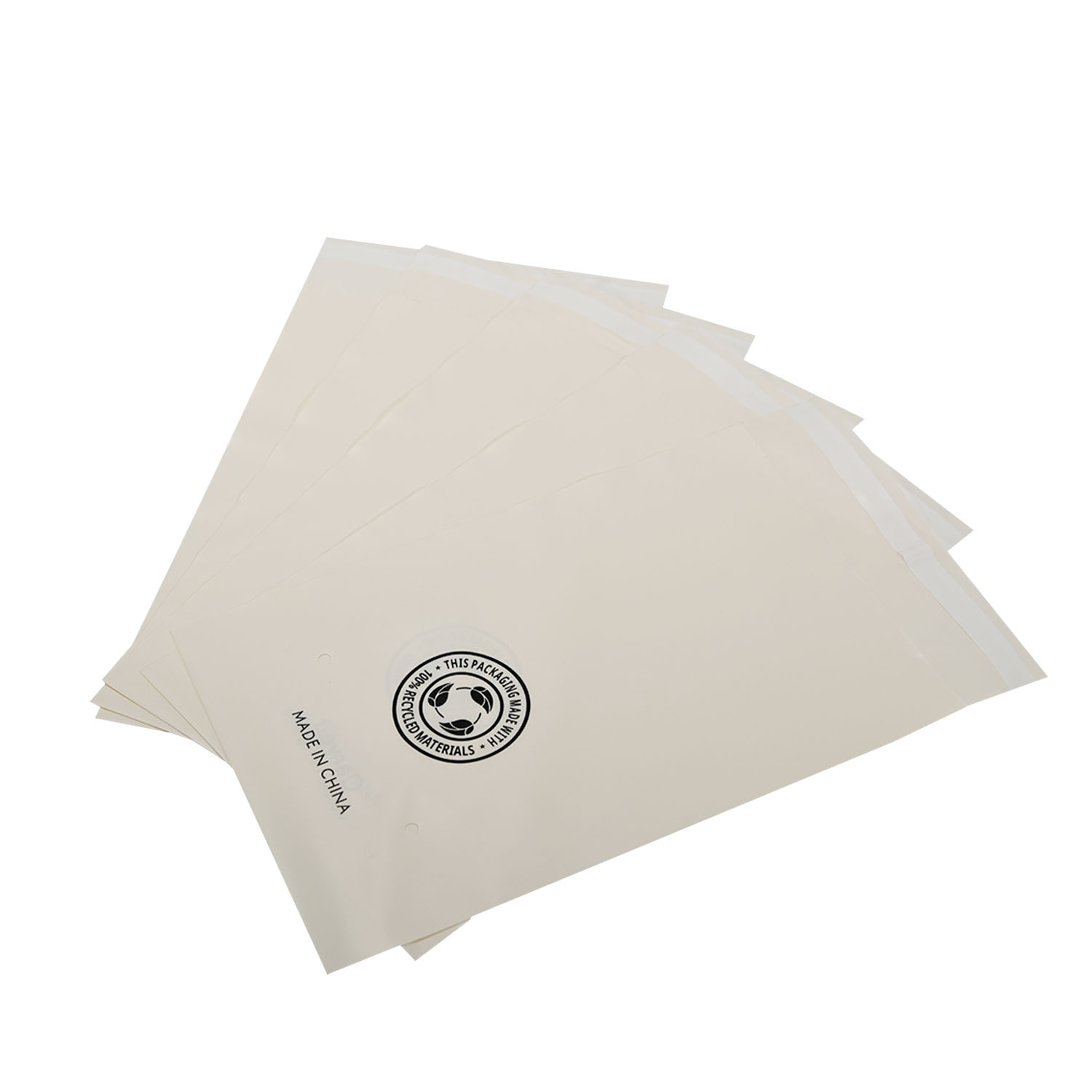